Plastic extrusion for high-strength, long-lasting materials
Plastic extrusion for high-strength, long-lasting materials
Blog Article
Discovering the Numerous Methods and Technologies Behind Plastic Extrusion
The world of plastic extrusion is a mix of technology, development, and precision, critical to numerous markets worldwide - plastic extrusion. Advanced machinery, computerized controls, and an array of products merge in this intricate process, producing high-quality, sturdy products. As the sector advances, a change in the direction of sustainable materials and smart equipment appears. The complying with conversation will certainly clarify these methods and innovations, while likewise hinting at the interesting future potential customers of this critical manufacturing procedure.
Understanding the Basics of Plastic Extrusion
The process of plastic extrusion, usually hailed as a cornerstone in the world of production, forms the bedrock of this discussion. In essence, plastic extrusion is a high-volume production process in which raw plastic material is melted and created into a continual account. The process starts with feeding plastic products, commonly in the kind of pellets, right into a warmed barrel.
The Duty of Different Products in Plastic Extrusion
While plastic extrusion is a frequently used technique in manufacturing, the materials utilized in this process considerably affect its final result. Different types of plastics, such as polyethylene, abdominal, and pvc, each provide distinct residential properties to the end product. Makers have to meticulously take into consideration the residential properties of the material to optimize the extrusion process.
Techniques Used in the Plastic Extrusion Process
The plastic extrusion procedure involves numerous methods that are crucial to its operation and efficiency (plastic extrusion). The conversation will start with a streamlined description of the fundamentals of plastic extrusion. This will be complied with by a failure of the process in information and an expedition of approaches to improve the performance of the extrusion strategy
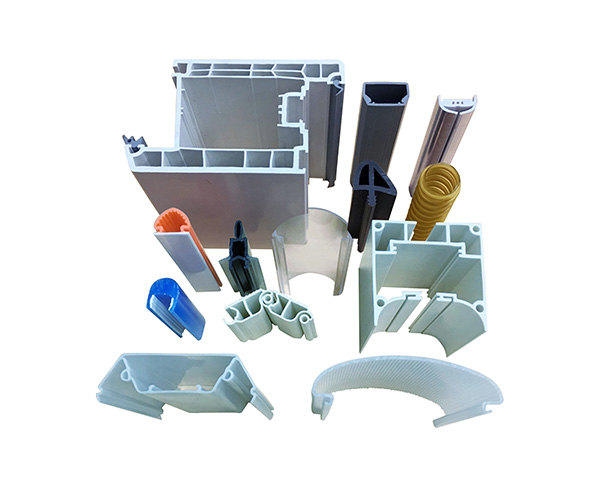
Recognizing Plastic Extrusion Essentials
In the realm of manufacturing, plastic extrusion stands as a fundamental procedure, important in the production of a plethora of daily products. At its core, plastic extrusion involves transforming raw plastic product into a constant profiled form. This is accomplished by melting the plastic, frequently in the kind of granules or pellets, and forcing it with a shaped die. The resulting item is a long plastic item, such as a cable, pipe, or panel finish, that preserves the shape of the die. This cost-efficient technique is highly flexible, able to produce intricate forms and accommodate a variety of plastic materials. Fundamental understanding of these basics permits further expedition of the extra complex aspects of plastic extrusion.
In-depth Extrusion Refine Failure

Improving Extrusion Method Performance
Efficiency gains in the plastic extrusion process can considerably affect both the high quality of the end product and the total click to find out more productivity of the operation. Continuous optimization of the extrusion technique is vital to preserving a competitive side. Methods that improve efficiency typically include accurate control of temperature level and stress throughout the process. Modern technologies, such as computerized systems and sensors, have actually contributed in accomplishing this control. Furthermore, making use of premium raw products can lower waste and enhance outcome quality. Regular upkeep of extrusion tools can also reduce downtimes, published here therefore raising efficiency. Embracing lean manufacturing principles can help get rid of unneeded actions in the process, promoting effectiveness gains.
Exactly How Innovation Is Altering the Face of Plastic Extrusion
The development of new technology has actually dramatically transformed the landscape of plastic extrusion. It has resulted in the development of advanced extrusion machinery, which has actually enhanced the performance and quality of the plastic extrusion procedure. Technologies in the extrusion process have actually also been driven by technical innovations, using enhanced capabilities and flexibility.
Advanced Extrusion Machinery
Revolutionizing the world of plastic extrusion, advanced machinery imbued with innovative innovation is ushering in a new era of efficiency and accuracy. These makers, equipped with cutting-edge features like automatic temperature level control systems, guarantee optimum conditions for plastic handling, consequently lessening waste and boosting product quality. High-speed extruders, for example, amplify output rates, while twin-screw extruders supply premium blending capabilities, vital for producing intricate plastic blends. Furthermore, electronic control systems offer extraordinary accuracy in procedures, reducing human mistake. Furthermore, these equipments are designed for long life, reducing downtime and upkeep expenses. While these improvements are currently amazing, the continual advancement of modern technology assures also better leaps forward in the field of plastic extrusion machinery.
Innovations in Extrusion Procedures
Taking advantage of the power of contemporary technology, plastic extrusion procedures are going through a transformative transformation. With the advent of 3D printing, the plastic extrusion landscape is additionally expanding right into new worlds of opportunity. These technical innovations are not just enhancing the top quality of extruded plastic products yet likewise propelling the market towards an extra lasting, effective, and ingenious future.
Real-World Applications of Plastic Extrusion
Plastic extrusion, a flexible and reliable process, locates Bonuses usage in plenty of real-world applications. It's mostly employed in the production market, where it's made use of to create a myriad of items such as pipelines, tubings, home window frameworks, weather condition removing, and fence. The automotive sector additionally harnesses this technology to produce components like plastic and trim bed linen. In addition, the clinical field depends on extrusion for the fabrication of catheters, IV tubing, and various other clinical gadgets. Also in food production, extrusion contributes in creating items like pasta or grain. The stamina and adaptability of plastic extrusion, combined with its cost-effectiveness, make it a crucial process across various industries, highlighting its extensive useful applications.
The Future of Plastic Extrusion: Predictions and Trends
As we look to the perspective, it comes to be clear that plastic extrusion is positioned for considerable innovations and change. Environment-friendly options to traditional plastic, such as bioplastics, are additionally anticipated to gain grip. These fads suggest a vibrant, developing future for plastic extrusion, driven by technical technology and a dedication to sustainability.

Conclusion
To conclude, plastic extrusion is an intricate procedure that makes use of innovative modern technology and varied products to create diverse products. Technical innovations, such as digital controls, enhance the production process and guarantee constant results. In addition, the market's concentrate on sustainability and intelligent equipment recommends a promising future. As plastic manufacturing remains to progress, it stays an important part of many industries worldwide.
In significance, plastic extrusion is a high-volume manufacturing process in which raw plastic product is melted and formed into a constant profile.While plastic extrusion is a generally used method in production, the materials utilized in this procedure considerably influence its final outcome. At its core, plastic extrusion involves transforming raw plastic product right into a continuous profiled shape. It has led to the development of sophisticated extrusion equipment, which has actually boosted the efficiency and high quality of the plastic extrusion process.In verdict, plastic extrusion is a complex procedure that utilizes advanced technology and differed products to develop diverse products.
Report this page